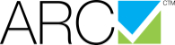


Examples of maintenance activities to increase reliability and minimise emissions:
• Assessing refrigerant charge
• Cleaning heat transfer surfaces
• Review of the installation for deficiencies
• Sealing/repairing of the cabin and system ductwork
• Logging and ongoing analysis of monitoring information – flows, pressures, temperatures, refrigerant leakage rate, etc.
Examples of maintenance activities to target refrigerant leakage would include:
Regular servicing should be conducted as per manufacturers’ recommendations and mine site maintenance policies.
• Regular visual inspections for oil sweating and signs of physical damage to system
• Regular monitoring of system charge through system pressure and pipe temperature analysis
• Completion of documentation relating
to system inspections
• Annual servicing or replacement of critical components
Leak detection processes
Leak detection should be conducted in conjunction with routine maintenance service procedures or commissioning of an air conditioning (AC) system or testing of an AC system post-repair (as per the Australian automotive code of practice).
Formalised leak detection procedures must be followed when system servicing and repairs are conducted (electronic, nitrogen pressure testing, bubble detection, dye detection etc).
This information is used as a guide only. Please refer to the air conditioning manufacturer’s recommendations for appropriate maintenance and servicing of your mobile air conditioning equipment.